ILPA Group has always focused on the continuous improvement of performance and technological advancement. With this in mind, the new Ilip storage and distribution center was designed and is being completed.
The opening of this structure will make it possible to concentrate the material currently located in five different facilities in a single logistics hub. This operation will reduce the need for transports from one facility to another, ensuring a significant drop in CO2 emissions associated with the logistics cycle.
The new structure was designed to allow the company to continue to guarantee the high standards of service already well known by ILIP customers even in the face of the significant difficulties currently present on the supply market. The new logistics center is a complex structure that makes massive use of automatic equipment such as stacker elevators, LGVs, anthropomorphic robots, automatic filming and labeling stations.
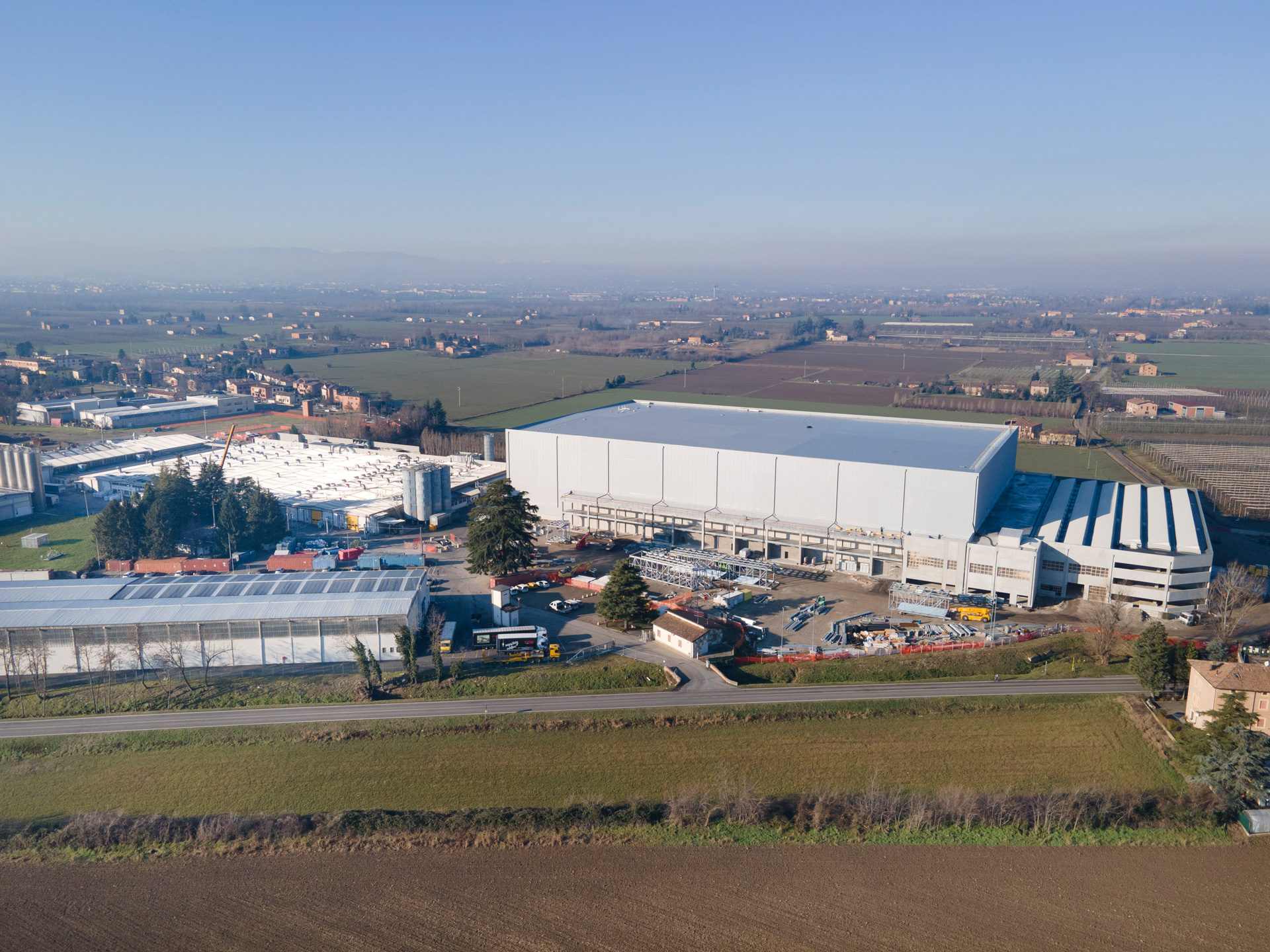
Storage area
The warehouse is sized to accommodate about 60,000 pallets in the 800×1200 mm format; cells have different proper heights between 2,500 and 2,950 mm and weights from 800 to 1,000 kg. The handling of the material inside the warehouse is carried out using twelve traslo-elevating robots. The warehouse features an oxygen depletion system to avoid the risk of fire.
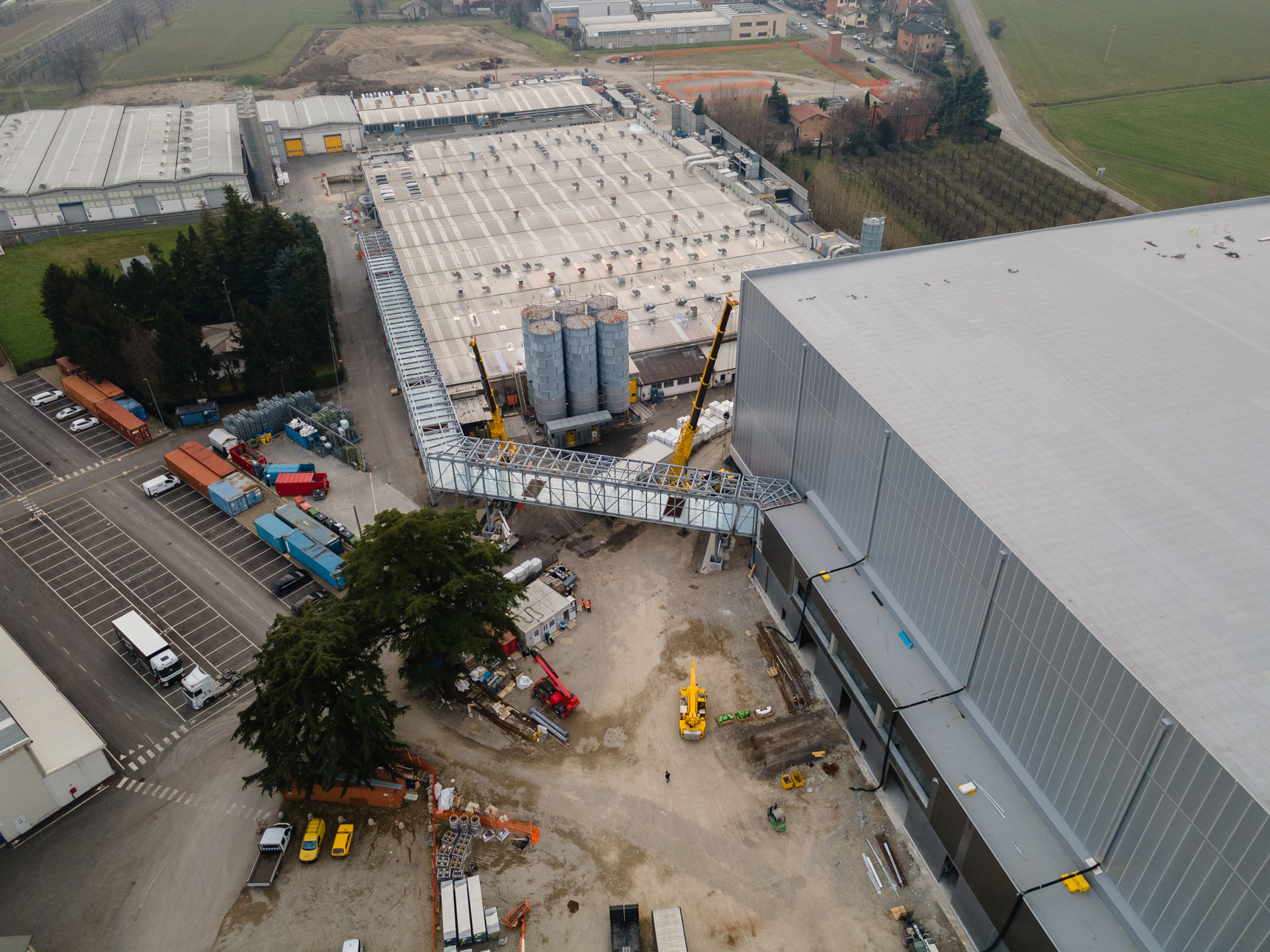
Building dedicated to handling activities
The ground floor houses an entrance bay with slave pallet automatism for 1200×800 with shape control, eight entire output bays per shipment, which ensure a capacity of two hundred and thirty pallets/hour. There are four manual picking bays on the first floor, an automatic picking bay that processes “carton layers” and an automatic filming station with a labeling machine. On this level, handling is fully automated and carried out through seven LGVs (Laser Guided Vehicles)
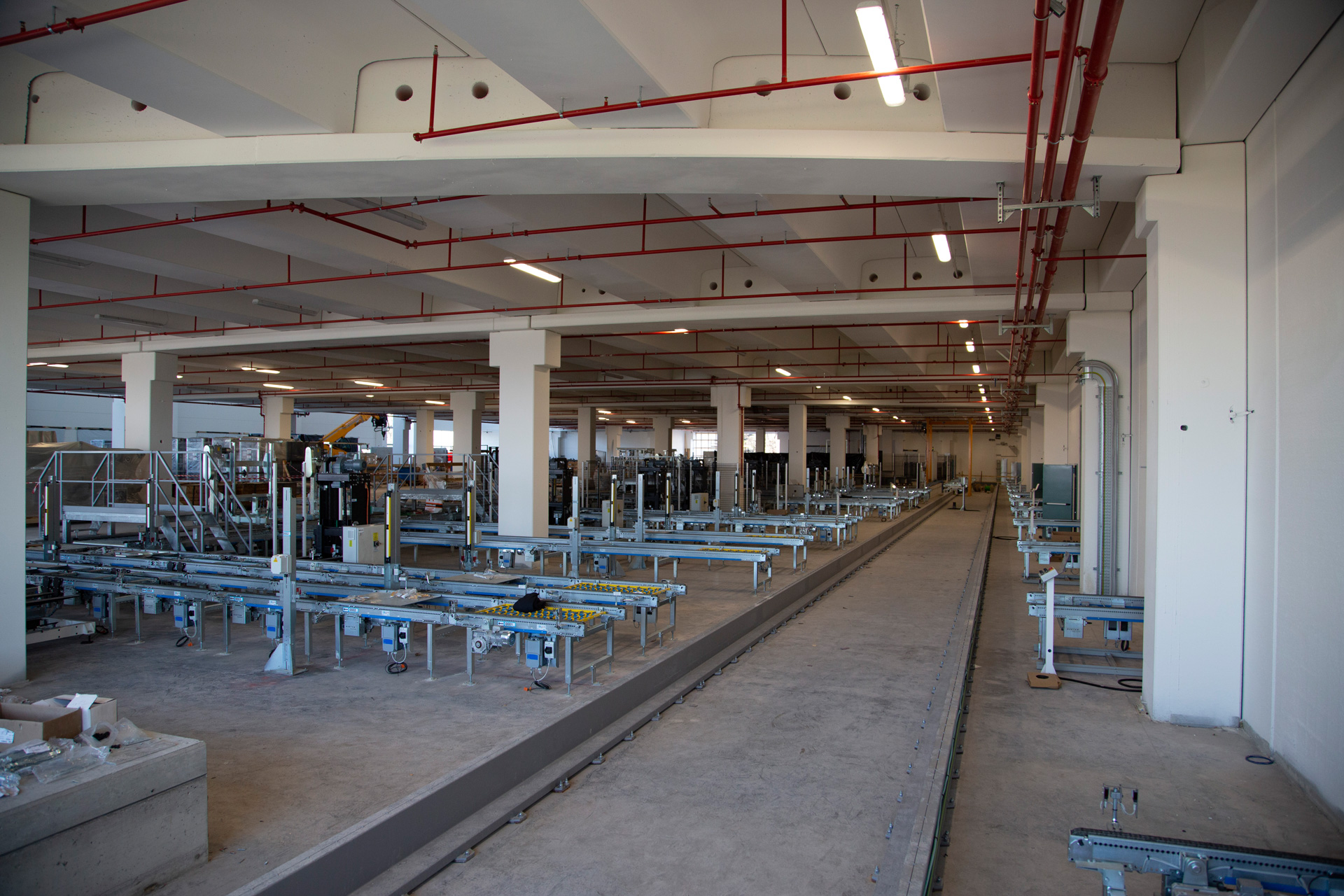
Aerial tunnel and loading/unloading bays in production
An overhead tunnel connects the automatic warehouse to the production plant; handling takes place via a monorail that creates a link between the warehouse and the two production sheds, ensuring a capacity of sixty pallets/hour in both directions. In addition, at each of the two production halls, there is a loading/unloading bay that, employing the connection made with the aerial tunnel, allows the finished product loading on the automatic warehouse and the production departments’ supply packaging materials.